The embedded computing market is broad and varied — and gets more so every day. Applications ranging from retail displays to aerospace components incorporate embedded computers, but with very different requirements in terms of form, fit, and function within the final product. So, the embedded system-on-module (SOM) market has responded with a diverse array of options. In this blog we’ll focus primarily on the fit, or mounting styles, available for SOMs.
Start with Surface Mount (SMT)
The physical specifications of a SOM module, including its size, shape, layout, and connection interfaces, play a key role in the adaptability, robustness, and performance of the module when it is fitted (or mounted) onto a finished product.
Three of the most common mounting styles are: board-to-board connectors, edge mount connectors, and surface mount technology (SMT). Within the surface mount format, there are a number of connectivity options, including land grid array (LGA), ball grid array (BGA), and castellated pads (also known as "castellated mounting holes").
SMT modules accommodate carrier board design complexity in a number of ways. First, the edge castellations (so named for their appearance like the walls of a medieval castle) are ideal for simpler product designs. The castellations help reduce the number of layers in the carrier board and provide cost-effective design integration, including the ability to hand-solder prototypes. For more full-featured product designs, the LGA and BGA mounting option provides complete design freedom and facilitates a reliable manufacturing process.
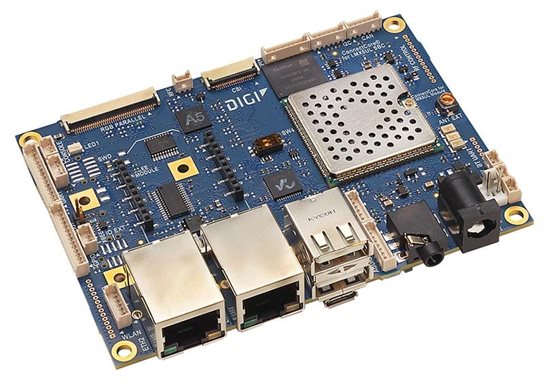
SOM Mounted on a Carrier Board
Digi uses a mounting system we call Digi SMTplus®, which combines two technologies in one. SMTplus offers both edge castellations to simplify the development of the carrier board and universal LGA pads to provide access to all of the functionality available on the SOM.
This design has been simplified and optimized to provide maximum flexibility, enabling developers to choose the configuration that best fits their product requirements. Digi SMTplus is designed for automated placement in both low-volume and high-volume applications to optimize cost. Additionally, it provides an optimal solution from a pin-count point of view. 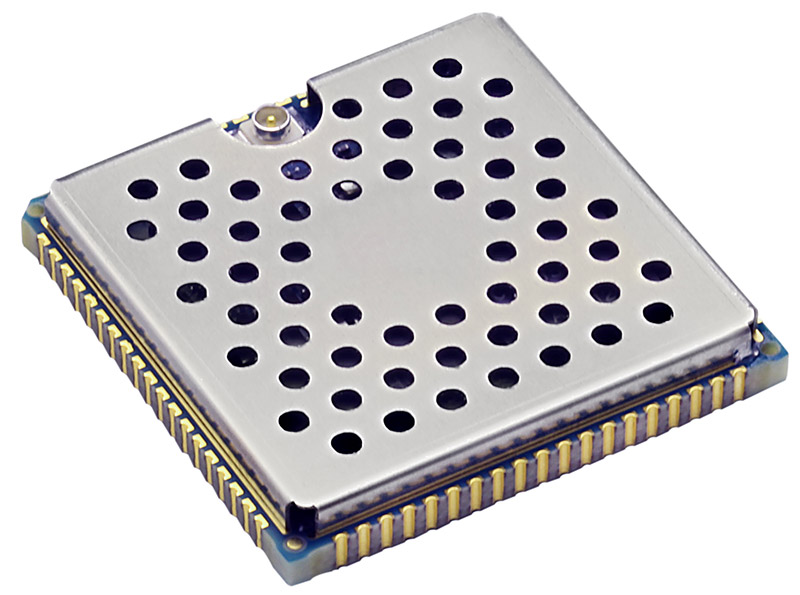
Digi ConnectCore 6UL with Digi SMTplus - Top View
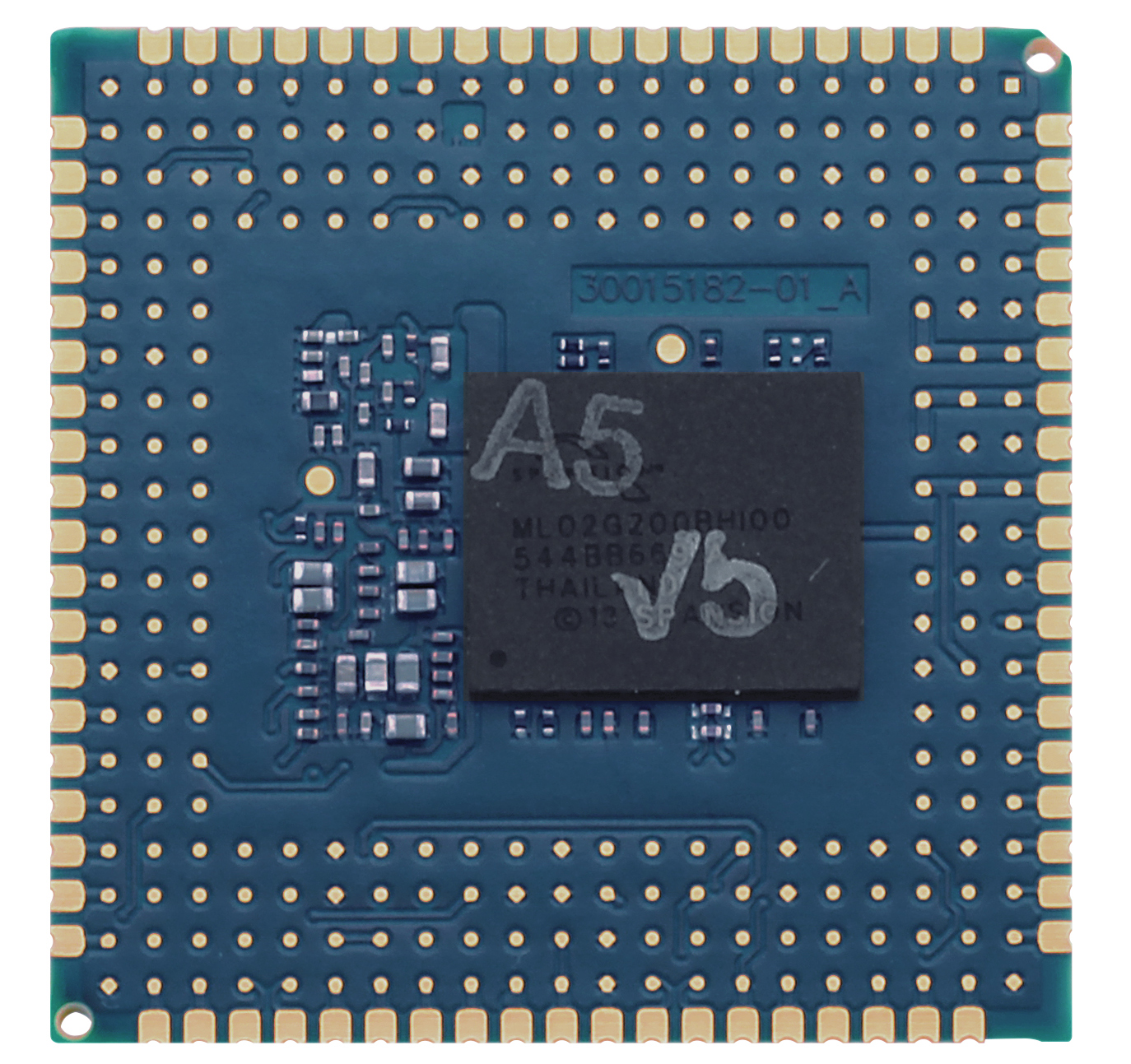
Digi ConnectCore 6UL with Digi SMTplus - Bottom View
SOM Mounting Considerations
It’s important to understand the characteristics, benefits, and drawbacks of the different mounting options when choosing an embedded format. Factors like size, connectivity, security, ruggedness, thermal performance, and connector type all impact ease of manufacturing and total cost of ownership. Let’s review some of these major considerations.
- Size and signal availability: SOMs with an edge connector (such as SO DIMM 200, 260) provide a good pin count/size ratio, but the number of pins can increase the length of the module to a point that is impractical. SOMs that have a lot of functionality to expose can do so with board-to-board connectors, which provide a better pin count/size ratio and are ideal for more complex designs. SMT mounting provides a good balance of pin count and size, allowing all of the functionality available on the SOM to be exposed while remaining a practical size for a range of product dimensions.
- Mechanical reliability: Many embedded products are deployed in harsh environments subject to intense vibration. The multiple solder joints of the SMT design provide superior mechanical robustness in these conditions. The low profile of a surface-mount module also contributes to overall mechanical strength. SMT modules can pass highly accelerated lifetime testing (HALT), vibration, and drop tests without incurring additional material and labor costs associated with fixing the module to the carrier board.
- Thermal performance: Based on an evaluation of the Digi ConnectCore® 6, SMT mounting exhibited the best thermal management performance. The reasons for this have to do with two ways in which the SMT format efficiently transfers heat: 1) the shield acts as a heat spreader, and 2) the SMT design effectively conducts heat to the ground plane of the carrier board.
- Electromagnetic immunity: SMT provides best-in-class EMI performance. Specifically, the Digi SMTplus design reduces the radiated emission from lead inductance and limits the size of the radiation loop area. Also, the use of a full shield covering the entire SOM reduces the radiation not just of the wireless interface but of the full module.
- System cost: Total cost of ownership (TCO), not just unit cost, should always be considered when evaluating embedded modules. If a module requires additional connectors, be sure to determine how much this will add to the total bill of materials (BOM) cost. For example, surface-mount modules don’t require a connector on the carrier board, while other designs may need one or more of these connectors. This can increase the final cost of a product by $2 to $3 (USD) per unit, not including attachment components such as screws and stand-offs or labor.
Mounting Style Comparison
The following table provides a comparison chart to help you evaluate a range of SOM features and mounting options.
Feature |
Digi SMTplus LGA |
SMTplus castellated |
Edge connector |
Board-to-board connectors |
Carrier board design |
Good |
Best |
Best |
Good |
Pinoutcount/size |
Best |
Better |
Good |
Best |
Mechanical robustness |
Best |
Best |
Good |
Good |
Thermal performance |
Best |
Best |
Good |
Good |
EMI |
Best |
Best |
Better |
Good |
For Long Product Life – Digi ConnectCore 8M Nano
The Digi ConnectCore® 8M Nano SOM, which is based on the NXP® i.MX 8M Nano application processor, employs the Digi SMTplus mounting format to maximize both reliability and design freedom. It is designed for the extended 10+ year product lifecycles of many embedded devices and helps OEMs lower their R&D and development costs. It also helps deliver a lower total cost of ownership by leveraging pre-certified wireless connectivity. The Digi ConnectCore® 8M Nano also offers remote management capabilities, as well as cloud integration and a complete Linux software platform based on Yocto Project.
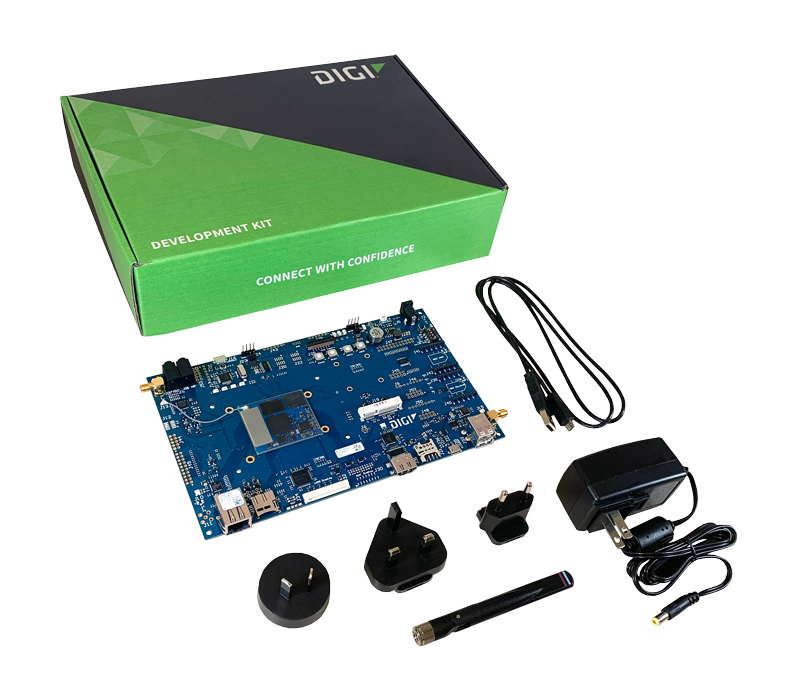
Digi ConnectCore 8M Nano development kit
Summary and Take-Aways
All mounting styles have their advantages and disadvantages. Considering all the factors—connector type, ruggedness, size, connectivity, ease of manufacturing, and especially total cost of ownership—will allow for maximum design longevity and future compatibility without compromising your ability to optimize the board design.
Contact Digi for help selecting the right embedded solution for your product vision. Digi teams can support you with any phase of your journey, from planning through development and production.